7:30 in the morning. A typical time at UNH where the quad is empty, Bartels is just waking up, and classes have yet to begin. But for students in the ASME organization, 7:30 has an entirely different meaning. Senior Michael Ingmanson and sophomores Matt Zwilling and Charles DiGuglielmo are on their way to meet with representatives from Vespoli USA, a manufacturer of world class racing shells.
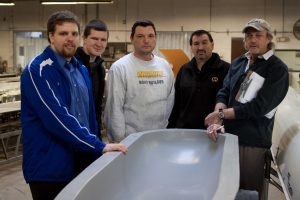
The group will be discussing the creation of a custom carbon fiber shell to be used in the University of New Haven’s super high mileage vehicle competition. This shell will play a key role in the success of this year’s cutting edge vehicle.
The UNH student chapter of the American Society of Mechanical Engineers competes annually in the supermileage collegiate design competition, organized by the Society of Automotive Engineers (SAE).
Held in Marshall, MI, the various teams run their vehicles around a 1.6 mile track of hills and turns, each team striving to achieve the highest possible fuel efficiency. The fuel efficiency of the competition, which is measured in miles to the gallon, is the primary focus of the building engineers. Ingmanson, the team’s captain, recalls how “the atmosphere is tense and energetic as higher scores get posted throughout the day.” The team from UNH is striving to have a vehicle that will move at 500 miles to the gallon. The competition will open in June.
During this year’s competition, the UNH team will unveil their second generation vehicle, a car which has been designed to be light, fast, and efficient above all else. Roy Pilletere, the senior chief design engineer overseeing the shells notes that “this year’s shell design has pushed both aerodynamic and weight factors to the extreme.” This year’s vehicle includes numerous modifications carefully designed to maximize the vehicle’s gas mileage, and is expected to reach a fuel efficiency of 500 MPG. The most important innovations include the use of high performance wheels, engine modifications, an electronically controlled throttling system, and the unibody carbon fiber frame and shell.
The students visiting Vespoli’s manufacturing facility discuss the shell progression with Walter Torres.Torres, Director of Operations and a 30 year Vespoli veteran, talks with the UNH team about mounting the engine and other critical components to the shell. When asked about the manufacturing process, Torres explains that an original 3D CAD drawing is used to produce life size foam model of a shell. This foam is then converted into a female mold, which is in turn used to make the carbon fiber shell. The process is long and complicated, but the 20 UNH engineering students working on the project are sure to understand the changes to the vehicle.
Vespoli, located near UNH, is helping the students design the shells needed for the high speed vehicle. With over 25,000 dollars in materials and donations, Vespoli engineers have worked extensively to help the ASME group achieve success at its second annual competition. A hearty thank you is extended to Vespoli for everything they have done for ASME, the Tagliatela School of Engineering, and the University of New Haven.
Curious about the work being done by ASME? Information can be found on the Vespoli website, www.vespoli.com, or the SAE website http://students.sae.org/competitions/supermileage/. Before the competition (Jun. 10 to 11), the high speed vehicle will be on display in Buckman Hall.